policy_2020_21
Navigation
Health and Safety Policy Statement September 2020
As Head of the Department of Chemistry, I accept my statutory duties to ensure (as far as is reasonably practicable) the health, safety and welfare at work of all the Department staff and students, and of other persons who may be affected by the Department’s undertakings.
My objective is to achieve and maintain health and safety standards in line with the Higher Education sector’s national best practice. The Department has adopted the Higher Education sector’s Health and Safety Management Profile ‘HASMAP‘ system as our health and safety management framework.
I would encourage all staff and students within the Department to set a high standard of safety by personal example, in order that all staff and students should adopt an attitude of mind which accepts good safety practice as normal.
This policy forms an integral part of the Durham University health and safety management system. As such, I will ensure that University Health and Safety policy is implemented within the Department of Chemistry. Responsibilities and arrangements for the effective management of health and safety in the Department are in line with USHA guidance document Leadership and Management of Health and Safety in Higher Education Institutions.
The Department of Chemistry is committed to:
- Compliance with relevant health and safety legislation.
- Provision of a safe and healthy working environment.
- Prevention of injury and ill health.
- Improvement of health and safety performance using measures of performance.
- Formal communication and active promotion of this policy to all staff and students.
- A formal and fundamental review of this policy in consultation with appropriate members of the workforce.
- Use of strategic plans and health and safety objectives.
- Making resources available for health and safety.
Professor Karl Coleman, Head of The Department of Chemistry
14 September 2020 (Review Date: 14 September 2021)
DURHAM UNIVERSITY
BOARD OF STUDIES IN CHEMISTRY
CHEMISTRY HEALTH & SAFETY POLICY – 2020/2021
Section A: Organisation, Responsibilities & Management
Organisation and Responsibilities
The Department occupies Office, Teaching and Research buildings and facilities based at on the Science site, Durham. Health and safety arrangements are managed by the Head of Department and the Department Management Team who are advised by a single Health and Safety Committee. The Chair of the Board of Studies, Professor Karl Coleman, has overall responsibility for safety within Chemistry facilities and for authorising persons to use those facilities and the equipment therein.
Usage of facilities and equipment is limited to employees and Emeritus staff of the University paid by the Chemistry Budget Centre, to students paying chemistry tuition fees or visiting on exchange programs, to employees of other centres engaged in collaborative contracts and to employees of other institutions who are Senate’s academic visitors. All users and visitors are required to avoid at all times any behaviour that introduces unsafe practice
Every member of the University community has a responsibility to achieve good health and safety (H&S) practice; this responsibility increases incrementally through the levels of the University line management structure.
University Council | Deputy Vice Chancellor and Sub-Warden | Heads of Department/Colleges | Managers and Supervisors | Staff and Students | Visitors It is the responsibility of all members of staff and students of the Department to ensure that they are fully familiar with the Safety Policies and particularly statements which affect their own working areas. All staff in a managerial or supervisory capacity are responsible for managing the health and safety of those they supervise.
All employees are personally responsible for:
- Taking reasonable care for their own health and safety and that of others.
- Not misusing anything provided for health and safety.
- Reporting all accidents, incidents and hazards and suggesting improvements.
Departmental Responsibility for Health and Safety
Health and safety is the responsibility of everyone. The Department seeks to ensure that health and safety accountabilities and responsibilities are clearly communicated. Health and safety accountabilities and responsibilities are in line with Higher Education Sector best practice as detailed in University Safety and Health Association (USHA) guidance document ‘Leadership and management of health and safety in higher education institutions’. The detail from the USHA guidance document is incorporated into the University Health and Safety Policy that the Department adheres to. The University Health & Safety Policy can be found on the Health & Safety Service (UHSS) web site.
The “Topic A-Z” link from that page provides further detail on key topics (UHSS Topic A-Z).
The Chemistry Health & Safety policy, revised annually, is read and signed by all staff, postgraduate students, masters-level students, and academic visitors who use Chemistry facilities. It is available online (in html and pdf formats).
Departmental Safety Role Holders
In addition to the core accountabilities and responsibilities described above, in order to manage key health and safety aspects in the Department, persons are allocated specific departmental safety roles. The responsibilities of the persons are in line with the University Health and Safety policy.
The Departmental Safety Coordinator is Dr John Sanderson. He acts as Chair of the Board’s Safety Committee (UHSS Topic A-Z/Health and Safety Co-ordinators). The membership of the committee (Appendix A) is posted on the Safety Matters noticeboard outside CG121.
Staff with Specific Safety Responsibilities
Role
Biological Safety Coordinator
Waste Disposal
Display-screen equipment
Electrical equipment
Inorganic research and teaching laboratories
Organic research and teaching laboratories
Physical research and teaching laboratories
Safety and Research Technician
Lasers and other non-ionising radiation
Manual handling
Staff Member
Dr Gary Sharples
Dr John Sanderson
Dr Bryan Denton
Dr Bryan Denton
Dr Phil Dyer
Dr John Sanderson
Dr Eckart Wrede
Dr Connor Sibbald
Dr Eckart Wrede
Dr Connor Sibbald
Room
CG240
CG112
MC008
MC008
CG114
CG112
CG142
CG004X
CG142
CG004X
Management Arrangements
Management Commitment and Engagement within the Department are explained within the policy statement, the Organisation and Responsibilities section of this policy and The University Health & Safety Policy (see above).
The Department has a Hazard and Risk Register and a Risk Profile document which inform the risk assessment process and risk based priorities. A number of Responsible Safety Objectives are being worked on to further improve health and safety performance. These are detailed in the safety Action Plan.
Section B: Emergency Planning
There is a University Management Standard on Emergency Planning and Management (MS9, UHSS/Topic A-Z/Emergency Planning).
The Chemistry Department has plans to manage critical incidents and procedures for immediate response / recovery. These plans are described in this section of the policy document and its appendices. Definitions used in the critical incident plan include:
Near Miss: an event not that does not harm or damage, but has the potential to.
Minor Incident: a separate, identifiable, unintended incident, that causes minor injury to a person, or damage to property that could result in injury or ill health.
Critical Incident: an unexpected event confined to one area of business i.e. a single College or single Department, which has the foreseeable potential to seriously disrupt the normal activities in that area of business and has resulted in or caused: serious harm to an individual; potential for harm due to damaged equipment or structures; reputational damage; significant damage to a building; significant financial loss; and loss of information or data.
Major Incident: any actual or anticipated event, or series of events, which significantly affects a number of Durham University students, staff or operations and where normal management arrangements are unlikely to be sufficient. The event may have resulted in a single death or an injury likely to lead to death or multiple major injuries.
Minor Injury: an injury sustained on University property or University business that requires the intervention of a First Aider, including minor fractures to fingers, thumbs or toes, contamination of the eye requiring use of an eye wash, minor burns (< 10% of the body), concussion, cuts or grazes caused by slips/trips.
Serious Harm: where due to an injury sustained on University property or business a student, staff member of visitor is unable to perform their normal daily activity for a period of more than seven consecutive days (not counting the day of the incident), or where the injured person is taken from the scene to hospital for treatment to that injury. It includes a significant fracture, amputation of a body part, permanent loss of sight, serious burns (> 10% of the body), scalping, unconsciousness, or any other incident that requires resuscitation or admittance to hospital for > 24 hours.
Contact Arrangements and Recovery Following an Incident
In the event of a minor incident or near miss, communication with the person involved and their supervisor will be undertaken verbally and/or by email by the departmental safety coordinator or the secretary to the safety committee.
In the event of a critical or major incident, communication with those directly affected will be by first responders and subsequently the Head of Department. Notification to others will normally be sent by email as soon as practical by the Head of Department or the secretary to the safety committee. This email will describe the current situation, what will happen next, and how individuals may be affected.
Specific details for emergency evacuations are in Section B, Part 2m. Out of hours evacuations and power failures are detailed in Section B, Parts 2p and 7g.
Fire Precautions
Responsibilities
A list of names of staff responsible for individual laboratories, and their contact details, is provided in the Chemistry Fire Box housed at the Security Lodge at the main entrance.
Training
Fire safety training is provided annually by the University Fire Safety Adviser to all new starters (staff, postgraduate students, masters-level students, and academic visitors) in the Department.
Refresher training for staff is provided by the University Fire Safety Adviser when required.
Training records are maintained by the Secretary to the Safety Committee.
Fire blankets and extinguishers are situated throughout the building. The types of fire extinguisher available include:
Foam (Beige band, for liquid fires).
Carbon dioxide (Black band, for liquid and live electrical fires).
Dry powder (Blue band, for metal fires, liquid and live electrical fires).
Personnel trained to use fire extinguishers should be familiar with the locations and types of extinguisher in their area(s) of work.
Replacement fire extinguishers are available from Estates and Buildings. When an extinguisher has been used please notify either Mr Paul Hofmann.
Emergency exits:
Should be kept free from storage, obstructions and combustible materials at all times.
Should open correctly. Fire exits and fire doors are checked during the safety audit (Appendix B).
Should have the correct signage displayed.
Make sure you know where the emergency exits are located. The location of emergency exits is discussed with new starters by line managers and research supervisors during the induction process.
Fire Wardens:
The Chemistry buildings are divided into Fire Zones. Each zone is allocated at least two Fire Wardens.
Each zone has a Warden’s box containing a high visibility jacket, a map of the building outlining the Fire Zone, a check list and a no-entry sign for placement at the external entry to the zone.
Actions to be taken in the event of a fire:
Tackle the fire only if trained and it is safe to do so.
Raise the Alarm at the nearest break glass call point In the event of an emergency.
Call the Fire Brigade (9999) followed by the University Emergency Number (43333) in order to advise security staff.
Evacuate the building. The emergency evacuation procedure is described in Section B, Part 2.
Proceed to the assembly point.
Other Arrangements:
Fire alarm systems are situated throughout the Chemistry building and are normally tested every Wednesday between 08.00 and 08.55. If the alarm sounds for more than 3 minutes, the building should be evacuated.
Notices stating the ‘action plan’ in the event of a fire are placed in all relevant rooms.
A general fire practice, which is organised by the Safety Administrator, is held at least twice a year to check the smooth operation of the emergency evacuation plan.
Where staff or students require assistance in the event of an emergency evacuation a PEEP (Personal Emergency Evacuation Plan) must be completed in consultation with the Departmental Safety Coordinator. Guidance and templates are provided by the University Fire Safety Advisers (UHSS Topic A-Z/Fire Safety/Guidance).
One laboratory, CG004, is fitted with gas alarms. The emergency response plan for CG004 is known by key members of the safety committee and trained users of CG004. The first stage alarm is a high-pitched continuous sound. The second stage alarm is a full beacon sound like a fire alarm. If the gas alarm sounds, security (ext 43333), the DSC, or the deputy DSC should be notified. Anyone in the immediate (audible) vicinity should leave the building by the nearest accessible exit that avoids going past the door to CG004. If an emergency evacuation of the building is required, the procedures documented below in Part 2 should be followed. The protocols described below in Parts 5 and 6 may also be applied.
In the event of a failure of the fire alarm system, notification will be sent to [email protected] with the action required. Fire wardens and members of the Safety Committee will also circulate to ensure that the appropriate information is communicated verbally.
For further information on fire safety and evacuation visit UHSS Topic A-Z/Fire Safety.
Special Arrangements for 2019-20: there will be a transition this year from the old system of dynamic fire warden allocation to the arrangements described above. In the period before Christmas 2018, the old system will continue to operate.
Emergency Evacuation Procedure
On hearing the alarm, where reasonably practicable, personnel should make their area safe (e.g., turn off heating mantles, ensure reactions are left in a safe condition) before leaving the building.
All personnel should vacate the building, by the nearest outdoor exit, as quickly and safely as possible, checking rooms are cleared as they leave. Those using teaching laboratories should normally consider the teaching laboratory fire exits as their primary escape route.
On leaving the building personnel must make their way to the nearest fire assembly point indicated by the FIRE ACTION notice in their room. A representative from any affected area(s) or room(s) should report to the main entrance (red atrium, by the Security Office).
The first Fire Warden to arrive at the Warden’s box in each zone should don the high visibility jacket and sweep that zone to ensure that all rooms have been vacated, ensure that items on the check list have been completed, and place a ‘no entry’ sign on the external exit from the zone upon leaving. The Chair of the Board of Studies (or nominated representative) should leave by, or meet at, the main entrance to communicate events as soon as possible.
Each fire warden will be responsible for moving people away from their assigned exit to assembly points and ensuring no-one re-enters the building until the alarm has been silenced AND PERMISSION TO RE-ENTER HAS BEEN ISSUED via the Incident Manager.
The first senior member of the Safety Committee (staff member with ≥ 3 years employment in the Department) arriving at the main entrance (red atrium, by the Security Office) should introduce themselves to security personnel and will put on the orange high visibility jacket, held in the Security Office, and become the Incident Manager, responsible for communication with staff, security and the Emergency Services.
The person who sounded the alarm should report to the Incident Manager (by the Security Office) as soon as possible.
Anything that could not be made safe must be reported at the main entrance to the Incident Manager, to a Chemistry Fire Warden, or a responsible member of Chemistry staff, so that the Emergency Services can be informed.
A member of Security should contact the University electricians immediately. The response time is approximately 5 minutes before 16:00. The response time increases to greater than 20 minutes when the engineers are on emergency call out after 16:00.
In the event of a false alarm the Incident Manager will instruct Security to silence the alarm. Security will liaise with the electricians, if available, to perform this task. The electricians will later reset the alarm and all other plant machinery that has been automatically shutdown during the alarm.
In the event of an incident that does not involve fire, such as a hazardous materials spillage, the Incident Manager or the Emergency Services may instruct Security to silence the alarm to enable responders inside the building to work without distraction to make the building safe. Silencing of the alarm in these circumstances DOES NOT mean that it is safe to re-enter the building. Fire wardens must not allow personnel to re-enter until instructed that it is safe to do so by the Incident Manager.
If no reasonable cause for a sounder going off can be found, a senior member of the Department (Chair of the Board of Studies or nominated representative) and the Incident Manager should make a joint decision on whether the alarm is false.
Following a real incident, when the area is safe, Security will inform the Incident Manager, who will then appoint individuals to notify the Fire Wardens that it is safe to enter the building once no-entry signs have been removed. Note that there may be a significant delay in the case of a real incident and personnel may instead opt to leave the area. In this case they MUST ensure that a responsible person will make their work area safe.
The Safety Administrator will check after the fire drills if anyone experienced any difficulties. Any personnel who do not leave the building during a fire alarm will be referred to the Safety Coordinator and/or Head of Department.
Estates and Facilities will be informed if any problems are reported.
Out of hours. Should the fire alarm sound outside normal working hours (07:00 to 19:00, Monday to Friday), personnel should vacate the building by the nearest available exit in accordance with points (a) and (b) of this procedure. Once outside, all personnel should walk around the outside of the building to the Security Office (red atrium) and await further instruction. Should any personnel choose to leave the site, they must still sign the out of hours book at the Security Office to indicate that they have left. Security staff will inform personnel if or when it is safe to re-enter the building.
Covid-19. In the event that an emergency evacuation is required, the arrangements described above still apply. The nearest evacuation route should be used. Social distancing should be maintained where this is possible.
First Aid
The persons currently qualified in first aid at work are listed with their photos on the Safety Matters board and online at:
Current_First_Aiders.pdfCovid-19. Until further notice, in order to obtain First Aid assistance, Security should be contacted (43333), giving details of the incident an its location. Security will use Channel 1 on the hand held radios to contact a First Aider.
First Aiders attending an incident will wear gloves, face coverings, and visors (if appropriate).
Specialist First Aid. The persons currently qualified in the treatment of cyanide poisoning and injuries from hydrofluoric acid are listed on the safety matters noticeboard, first-aid boxes and the Chemistry Safety website.
The first-aid boxes are checked and replenished by Miss Kerry Strong. A list of all first aiders including specialist first aiders can be found on the front of each box.
Injuries of a more serious nature are referred to the Accident Unit of the University Hospital of North Durham. Transport should be by ambulance for serious injuries, or by taxi. Security office staff will assist with arranging a taxi.
Out of hours. In the first instance, if first aid is needed outside normal working hours, the security office (43333) should be contacted. Members of security office personnel are trained in first aid at work.
Accidents, Incidents and Near Misses
All accidents, incidents and near misses that could have led to serious injury or fires MUST be reported using the appropriate form. Serious accidents, dangerous occurrences and life threatening incidents must be reported to the Health & Safety Office immediately using Incident report (IR1) forms. Blank IR1 forms are kept in CG018. The log at the front of the book should be updated whenever an IR1 form is completed. Please inform Lizzie Amies when IR1 forms need to be replenished. Serious accidents, dangerous occurrences and life threatening incidents must be reported to the Health & Safety Office immediately. Following an incident in a teaching laboratory, a staff member who was working in the laboratory at the time should complete the IR1 form. Following an incident in a research laboratory, either the person involved, or a witness to the accident, or the research supervisor, should complete the IR1 form. IR1 forms for all other incidents should be completed by the line manager of the person(s) involved. Completed IR1 forms should then be handed to one of the currently serving reporting officers: Dr Connor Sibbald and Dr John Sanderson.
If an incident leads to any personal contact with a substance, it should be dealt with immediately, by safe and effective decontamination. A Diphoterine® MICRO DAP is available in each First Aid box to help with relieving the effects of acid or alkali splashes on the skin or eyes. This is suitable for splashes that cover no more than 3% of the body surface and should be used within 1 minute of the splash. See Appendix H for more information. If Diphoterine® is unavailable, risk assessments and safety data sheets should be consulted for details of treating exposure. In most cases, this will involve washing liberally with water.
More trivial near misses that are not immediately life threatening can be reported verbally or by email to a member of the Safety Committee, or by completion of a simple form online at: near_miss.
Procedure Following a Hazardous Material Release or Spillage
Immediately following an incident, the following steps should be taken:
evacuate all non-essential personnel from the immediate area around the incident and place a barrier or sign to prevent people re-entering the area;
if anyone has been injured, provided that it is safe to do so, follow the first aid procedures described in the departmental policy
(contacts);if the incident involves a fire, major release of volatile toxic or flammable materials, or an ongoing leak of flammable gases, the fire evacuation alarm should be sounded and the standard emergency procedures adopted (Tel. 9999 for the Fire Brigade, 43333 for the University emergency number);
if the incident is a spillage that is not spreading rapidly, is not endangering people or property except by direct contact, and does not endanger the environment, deploy the spillage response measures identified in the risk assessment;
once the spillage has been made safe, inform the Departmental Safety Coordinator or Safety Committee Chair if there has been any damage to property, a spill kit has been used, or there has is material that requires disposal. Contaminated waste should be disposed of by the usual routes (Section I). Spares for spill kits are available from stores;
notify personnel when it is safe to resume work in the area;
complete an IR1 form (even if the incident was a ‘near miss’).
If any of the following conditions apply, all personnel must be cleared from the area around the incident and a member of the Chemical Hazard Response Team (CHRT) called:
the material released or spilled cannot be identified;
the material released is a gas that is non-flammable and is still being released but not spreading beyond the area of the incident;
personnel experience any of the following toxic effects as a result of the incident: breathing difficulties, skin irritation, eye irritation.
How to contact the CHRT: The best method to raise the alarm is to phone security (42222) and ask them to contact the Chemistry Hazard Response Team (radio channel 1). Alternatively, a list of members of the CHRT, together with their contact details is posted at each of the three locations where the apparatus is located, just off the central landing on the ground floor, first floor and second floor of the main chemistry building. The following have been certificated for use and general inspection of the sets:
Mr Douglas Carswell, Dr Philip Dyer, Mr Paul Hofmann, Mr Malcolm Richardson and Mr Paul White, from 12/1/2017.
Dr Matthew Kitching and Mr Peter Stokes, from 27/4/2017.
Miss Kerry Strong, Dr Connor Sibbald and Mr Gary Oswald from 7/11/2018.
Covid-19. Until further notice, the Chemical Hazard Response Team is suspended. In the event of a spillage, follow steps (a) to (g).
Dealing With Spillages
Spillages must be dealt with immediately. Spill kits should only be used when they have been identified as the most appropriate and safe means for dealing with a spillage.
Solids and Liquids: In most cases, appropriate methods for treating spills of liquids or solids will involve either the use of a spill kit, or deployment of a substance to neutralise the spillage before disposal. Guidelines are given in the table below. Note: these are general and not a substitute for consulting safety data sheets and other sources of information. It is the responsibility of the researcher to make sure that appropriate neutralising agents are available before commencing a procedure.
Acids
Alkalis
Hydrocarbons
Mercury
Reactive metals
Other liquid
Other solidNeutralise with sodium bicarbonate
Neutralise with citric acid or ascorbic acid
Spill Kit
Consult Mr Paul Hofmann (policy, Code of Practice I)
Inert adsorbent (e.g. sand)
Consult SDS; Spill Kit
Materials in a fine dusty form should not be cleared up by dry brushingGases. In many cases, the most effective means of dealing with the release of a gaseous material is to isolate the source of the gas and allow the local exhaust ventilation to clear the release. However, this should only be undertaken if it involves no risk to any personnel in the laboratory. In all other cases, the area should be evacuated and the procedures documented below followed.
Spill kits (Ecospill, 15 litre) are provided for all locations where chemicals are stored and manipulated. A larger capacity spill kit is available in the COSHH room (CG018) if required.
Biological spill kits are available in all laboratories where GM work is undertaken. All workers in these laboratories should either be trained in their usage, or be supervised by somebody who has been trained. A code of practice for use of the kit is in each box.
The Ecospill kits are packed in distinctive yellow holdalls. Each kit contains:
1 Absorbent boom for use to contain a spill.
8 Absorbent pads for use directly on a spill for absorption
2 Hazardous waste bags & ties for disposal of contaminated booms and pads.
1 Instruction leaflet.
The pads and absorbent boom are of the yellow ‘Chemical’ or ‘C’ type for spills involving water, oils, and aggressive liquids (i.e. acids and bases). These kits do not contain chemically-resistant gloves, acid/base neutralising agents and other equipment such as a dustpan and brush or pH paper.
The British Standard colour coding for absorbents is:
Maintenance, Grey/Black (M): for use inside on spills of non-aggressive water and oil-based fluids and mild chemicals.
Oil Only, White (O): for the preferential absorption of oil-based liquids on land or water, including vegetable oil, mineral oil and most hydrocarbon derivatives.
Chemical, Yellow (C): for use on spills of aggressive liquids i.e. acids and alkalis. Can be safely used on water- and oil-based spills. For use on land only.
An absorbent compatibility guide is given in Appendix F.
Procedure for using a spill kit:
Before using a spill kit, make sure that it is appropriate for the spillage to be treated, considering the chemical compatibility of the adsorbent and SDS for the spilled material(s). This should have been considered as part of the risk assessment before starting a process.
Appropriate PPE (gloves, lab coats, safety glasses, footwear) must be worn, in accordance with the departmental safety policy on Good Laboratory Practice (GLP, Code of Practice A). The SDS and risk assessments for the material(s) involved must be consulted beforehand.
Spills involving hazardous materials should first be contained if necessary using an absorbent boom (also referred to as a sock) or pad (also referred to as a pillow) to prevent spread of the material to other areas. Special attention should be paid to preventing the material from reaching any drains.
Working from the outside in, the spilled material should either:
be absorbed using one or more absorbent pads; or
be neutralised with an appropriate agent (e.g. citric acid for bases, sodium bicarbonate for acids). Once neutralised, absorbent pads should be used to clear remaining liquids.
Once absorbed, the treated material should be placed into a hazardous waste bag and sealed with a cable tie; this bag should then be placed inside a further bag (‘double bagged’) and again sealed with a cable tie.
The material should then be removed to a safe place for disposal in line with the departmental safety policy on waste (Section I), or further treatment as appropriate.
The parts of the spill kit that have been used should be replaced from stores.
Power Failure
In the event of a power failure, fume cupboards and air handling will no longer function. No work should be conducted in synthetic or teaching laboratories under these circumstances. Personnel may remain in offices and write up areas where there is no chemical hazard for as long as necessary, provided that there is sufficient illumination and the fire alarm is not sounding. In the event that there is insufficient light, you should leave the building.
Supervisors are responsible for ensuring that measures are in place to protect the safety of researchers in their laboratories in the event of a power failure. In undergraduate teaching laboratories, senior demonstrators are responsible for ensuring the safety of undergraduate students and junior demonstrators.
Telephones. Should the network also fail, IP telephones will no longer function. In order to report the power failure, summon assistance, or report an emergency, use one of the red emergency telephones.
In the main building, these are located on each floor in close proximity to the lifts. One is also located at the back of the physical chemistry teaching laboratory (CG127).
In the materials chemistry building, one is located in the communal area by the entrance opposite the Calman lecture theatre block, and one is next to the entrance from the courtyard.
Emergency lighting. In the event of a power failure during the hours of darkness, most laboratories and main circulation spaces have emergency lighting that should automatically trigger. This power is expected to last for up to 3 hours. If power has not been restored after 3 hours, the building should be vacated. Do not remain in areas without emergency lighting.
Fire alarms. The fire alarm system has an emergency power supply and should therefore continue to function in the event of a power failure. Unless you hear the fire alarm, there is no immediate need to leave the building. This emergency supply lasts for 24 hours. If the power has not been restored after this time, you should not re-enter the building until you are informed (by email) that it is safe.
Lifts. If a lift has an emergency telephone, it should still work during a power failure. If you are trapped in a lift during a failure, inform Security using this phone. If this method fails, and the alarm button in the lift does not work, make yourself heard by making a loud noise or shouting.
If you hear someone in a lift, contact Security using the emergency phone nearest the lift. Do not leave unless remaining is hazardous to your own safety; remain and communicate with the person in the lift to provide reassurance until either a member of Security staff or the Departmental safety team arrive.
In laboratories, following a power failure:
make experiments safe. At the socket, turn off all heating apparatus and equipment that may pose a safety risk, or be damaged by a surge, when power is restored;
seal solvent Winchesters and cover or seal all vessels containing volatile solvents to avoid an accumulation of toxic/flammable vapours;
if a vacuum line has a liquid nitrogen trap: turn off the pump at the socket, isolate the trap from the rest of the line, remove the nitrogen and then open the trap to the air. Do not leave traps cooled by liquid nitrogen open to the air, or under vacuum. Do not leave a sealed system containing volatile liquids;
avoid opening fridges and freezers if possible and do NOT turn them off at the socket;
leave the laboratory.
Long power cuts. Supervisors are responsible for sensitive materials in their laboratories, including those placed in fridges, freezers and glove boxes. Emergency power supplies from a backup generator are available in some locations. These are low power for systems such as fridges and freezers. Supervisors are responsible for provision of the appropriate cables to use these emergency sockets. Emergency sockets are normally powered from the normal mains supply. In the event of a mains power failure, the power will disappear until the generator starts. This can take up to 30 seconds. They are then powered by the generator.
Out of hours power cuts. General power failures that occur out of hours will be reported by email. During normal working weeks, overnight failures in specific parts of the Chemistry buildings will be reported by Security staff using the green forms on laboratory doors. If power fails to return within a short period, research supervisors are responsible for ensuring that any sensitive items are made safe.
Brown outs. In the event of a short-duration power outage, work may continue as normal after running equipment has been checked. Particular attention should be paid to ensure the correct operation of any equipment that either:
contains a printed circuit board; or
is thermostatically controlled, including hot plates.
Power resumption. When power has been restored, gradually turn electrical items back on. If you think any equipment is not functioning correctly, turn it off at the socket and inform the electrical workshop.
Incidents involving Metal Sharps (‘Needlestick’ Injuries)
In the event of an incident involving needles or other sharps:
Any injury caused by a contaminated sharp must be dealt with immediately.
The wound should be encouraged to bleed and then washed thoroughly using soap and water. If appropriate, cover with a waterproof dressing.
In cases where the sharp has been used with biological agents (e.g. blood or body products):
Any visual contamination with blood or body products to broken skin should be washed immediately with soap and water.
Any contamination of the conjunctivae or mucous membranes (mouth/nose) should be rinsed thoroughly with copious amounts of running water.
All such incidents should be reported immediately to the line manager/supervisor and an Incident Report form IR1 completed.
If possible, the source of the blood or body fluid should be identified in the event that testing is required for evidence of infection.
If it is known to have been an “infected” or “high risk” sample, the injured person should be advised to attend their own General Practitioner for further advice, counselling and possible treatment.
If the “source” is unknown then it should be regarded as “high risk”.
All staff working with blood and body products must know this procedure.
Ensure that all staff who are working with blood and body products are vaccinated in accordance with University Policy.
In cases where the sharp has been used with chemical agents:
Any visual contamination to broken skin should be washed immediately with soap and water.
Any contamination of the conjunctivae or mucous membranes (mouth/nose) should be rinsed thoroughly with copious amounts of running water.
The incident should be reported immediately to the line manager/supervisor and an IR1 Incident Report form completed.
If possible the sample should be identified. If it is known to have been a “high risk” sample, the injured person should be advised to attend Accident and Emergency with information about the accident for possible treatment.
Section C: Risk Assessments
Before beginning work in Chemistry facilities for the first time, each person must complete a personal
health and safety record (form PR1). This form includes a description of the planned project work and identifies the training, risk assessments
and other documentation required. Undergraduates are included at the start of their final-year project, if undertaken. For laboratory work a
project risk assessment must be completed before work commences. Two forms are available for this purpose, form CRA1 for the risk assessment,
and form CRA2 for project COSHH assessments. The researcher must be able to produce the countersigned form(s) on request (see also Code of
Practice A, Part 2(b)). All forms are available from the Chemistry Safety website:
Forms.
In addition, researchers undertaking biological projects should complete a risk assessment using the forms on the Department of Biosciences website:
https://www.dur.ac.uk/biosciences/local/staff/safety/.
A new PR1 form is required for existing workers who take up new contracts or change supervisors, or where there is a significant change in their work. For laboratory work, a new project risk assessment (forms CRA1/CRA2) must be undertaken before the new project is started. Any other training and documentation requirements identified in PR1 form should also be completed.
The following matrix is provided by UHSS to assist with making risk assessments:
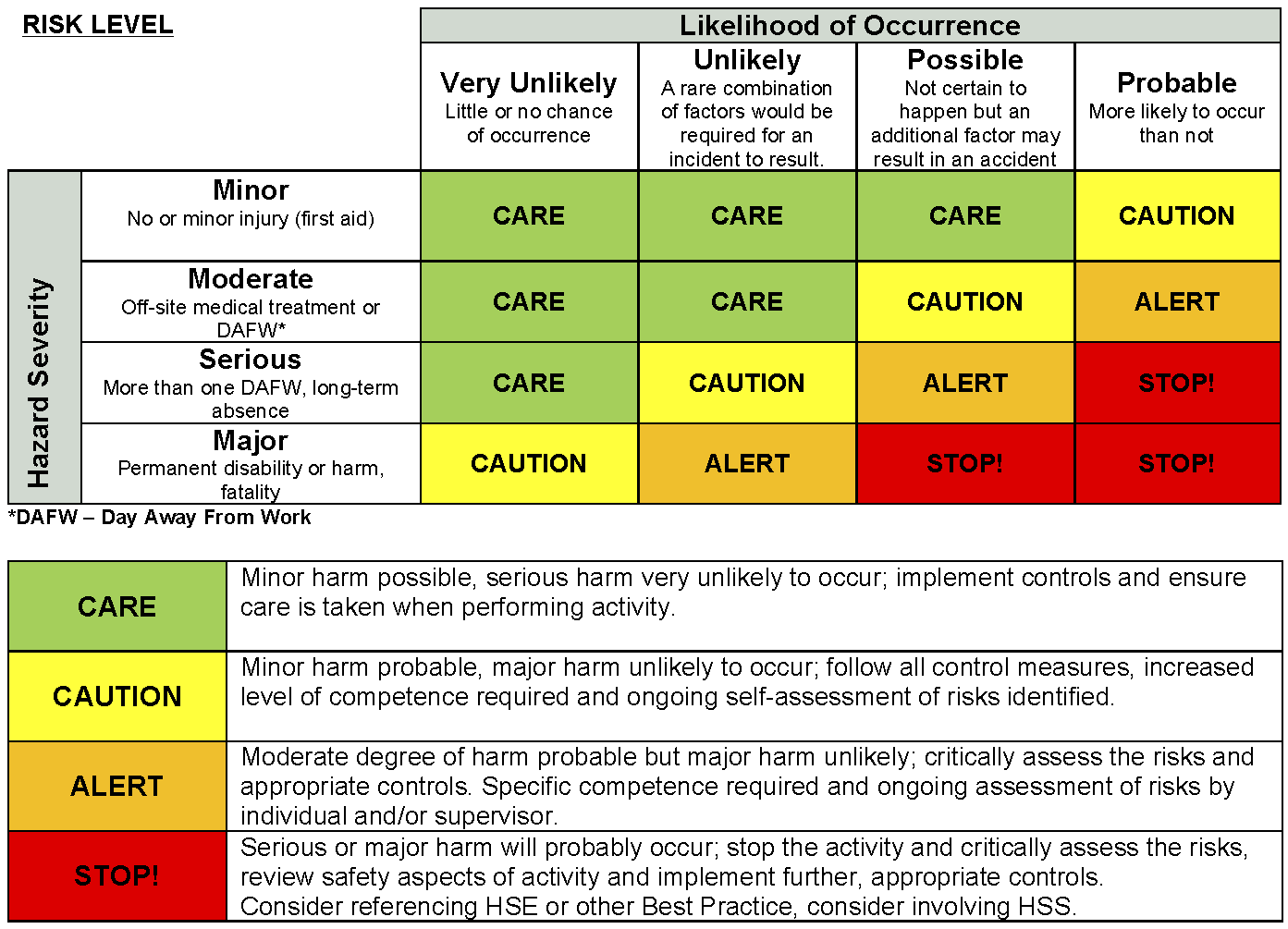
A risk assessment for general work in the department (Ref: CGRA2020) is available here. Note that:
by signing the policy, you accept that you have read and understood this risk assessment, and agree to implement the required controls;
separate risk assessments will be required for work extending beyond the scope of the general assessment.
this assessment does not contain all the Covid-19 measures. The Covid-19 risk assessment is in Appendix I.
All new projects (form PR1) must be endorsed by the Departmental Safety Coordinator, Chair of the Board of Studies, or in their absence, a member of the Safety Committee with the relevant expertise and experience to approve the project. Forms awaiting endorsement should be emailed to [email protected].
A risk assessment must be made for all work and work-related activity conducted in the Department. These assessments may involve one or more of the following:
The general risk assessment for work in Chemistry (Section C, Part 1, above).
The Covid-19 risk assessment (Appendix I).
A project risk assessment for laboratory work (form CRA1), including COSHH (form CRA2) if appropriate, for repeated work activities.
A risk assessment associated with a code of practice or a standard operating procedure (SOP) for a process or activity.
Individual assessments in laboratory or electronic notebooks for one-off experiments.
Covid-19. Consideration should be given to the following when planning experiments:
Social distancing measures may be required at short notice. Experiments that present a high risk should an experimentalist be unable to return will require contingency planning. The DSC and/or the safety committee chair should be consulted in such circumstances.
The Chemical Hazard Response Team may not be available.
Anyone authorising a risk assessment must have the necessary skills, experience, training and knowledge to manage health and safety and critically assess the work described in the assessment. Those conducting the task(s) in the assessment must have the skills required to complete the task(s) safely. The competencies for each role should be included in the risk assessment (see Section C, Part 4(a) ). More information is available from the UHSS (UHSS Topic A-Z/Training and Competency).
Competencies for authorising risk assessments in the Chemistry Department are outlined below:
Risk Assessment
General assessment for work in the Chemistry Department (Section C)
Risk assessments for research activities (experiments, processes, codes of practice)
Risk assessments for Special Codes of Practice
Risk assessments for undergraduate laboratory classes
Risk assessments for technical services and workshops
Those Competent to Authorise
Head of Department
Research supervisors with relevant expertise and experience
Nominated representative indicated in Section L of this document
Academic members of the safety committee with relevant expertise and experience, academic laboratory leaders
Technical service managers
Anyone who does not have the skills to complete a task safely should seek an alternative approach or ensure that the training required for the task is undertaken.
Competency Levels.
Level 1: Can train others and work without direct supervision. The individual has sufficient training, experience and technical knowledge to train others to conduct particular techniques, processes and use of equipment effectively and safely. This includes identification of hazards, assessment of risk, and identification of appropriate control and emergency measures. All risk assessments must be authorised by someone with Competency Level 1.
Level 2: Can work without direct supervision. Has had sufficient training or experience to demonstrate a level of technical competence, including the identification of hazards, assessment of risk, and identification of appropriate control measures.
Level 3: Can work supervised. An individual has basic knowledge of technical aspects of the task but needs supervision and hands-on training from someone with Competency Level 2 or better to reinforce the key aspects and ensure safe operation. Most undergraduates are in this category.
Level 4: Level 4: Can observe and participate. Requires close supervision from someone with at least Competency Level 2. Summer students of school age are typically in this category.
The competency level is task-dependent. For all tasks it is expected that the supervisors will be of competency Level 1. Most postdoctoral researchers and postgraduate students will be at Level 2 for the work they undertake, undergraduates will be at Level 3 and school-age summer students will be at Level 4. Risk assessments should assess the competency of those undertaking and supervising the work. If a risk assessment identifies that an individual does not possess the correct attributes to conduct work safely, either the task should be amended or suitable training and observation undertaken.
Assessment of competency: competency can be assessed using a number of criteria. Some of these include the level of experience and qualifications of an individual, and their employment status. Note that:
a record of attendance at a training session for a particular task, or the successful completion of a course of study related to the task, is not guaranteed to provide evidence of competency for that task;
skills decay over time, so an individual may no longer be sufficiently competent to carry out a task for which they once had the requisite level of competency. In this instance, competency should be reassessed and retraining undertaken if required.
The following are useful means of competency assessment in the Chemistry Department:
Observation. Undertaken continuously as part of day to day work by a supervisor (usually with Competency Level 1) and includes:
direct evidence, such as the checking of risk assessments or direct observation;
indirect evidence, such as the assessment of the performance track record of an individual; and
third party evidence, such as verbal feedback from colleagues.
In some cases competency may be assessed against performance standards. Observation also forms the basis for assessing competency during emergency measures (e.g. fire drills).
Set tasks or tests. Can be useful as part of an interview process, or as part of undergraduate training (e.g. conducting a risk assessment). In some instances it may be desirable to retest individuals with key roles at regular intervals.
Oral questioning. Useful as part of an interview process (e.g. to establish whether an applicant is competent to work safely on a particular task).
Qualifications and Role. Although not direct evidence of competency, a minimum level of academic achievement and job seniority is usually required for each competency level. For example, risk assessments for research would normally be authorised by academic staff with training to at least PhD level.
Evidence needs to be relevant, authentic, up to date or recent, and sufficient to make an appropriate judgement.
An assessment of the hazards associated with work in the Chemistry Department is in Appendix C. Please note that:
Appendix C is an assessment of hazards, not risks. The risk level for any particular work will depend on the details of the project (e.g. scale), other activity in the location where the work is to be carried out (e.g. who else will be affected), and other details specific to the location (e.g. room size, services available).
The hazard assessment in Appendix C and the risk assessment in Section C (Ref: CGRA2020), and Appendix I, form the basis for the rest of this policy.
Section D: General Safety Arrangements
The Safety Matters board is located on the First Floor landing just past CG121. Staff will be informed by e-mail and through the Safety Website about amendments to the University Health & Safety Policy and the issue of new University Health & Safety notes.
Reporting Concerns.
The Department operates a policy towards whistleblowing that is in accordance with The Public Interest Disclosure Act 1998. This protects the rights of workers against detriment or dismissal after raising concerns on dangerous activities with the enforcing authority (HSE), and encourages the resolution of problems within the workplace before they are raised externally.
You are strongly encouraged to report any matters that endanger the safety of any individual. You should report your concerns to one of the following, listed in order of preference:
your line manager or supervisor;
a member of the Safety Committee (Appendix A), either in person, or by email to [email protected];
the Chair of the Board of Studies ([email protected]);
the University Health and Safety Service ([email protected]).
If for any reason you cannot disclose your concern to one of these, e.g. because it implicates them, or if you are not satisfied with the response to your concerns once raised, you should use the next contact in the order of preference.
Anonymous reporting. Concerns expressed anonymously may be harder to verify, but will be considered at the discretion of the UHSS, particularly if they are of a serious nature. An online form for anonymous reporting of safety concerns to the UHSS is available on the Chemistry Safety website. Information entered into this form is sent by anonymous email. No information about the sender is included in any part of the message, including the header. The form can be accessed at:
anon_reporting.False reporting. Any reporting that is intentionally false or malicious may result in disciplinary action being taken.
Response to a concern. The action taken after a concern has been received will depend on the nature of the concern. Anything that is an immediate threat to life, or is assessed as having a high probability of leading to injury, will be classed as ‘serious’. Serious matters, once verified, will be taken up with the personnel involved and their line manager, if appropriate. Remedial action will then be agreed. Less serious matters, such as minor infringements of the safety policy or minor infrastructure problems, will usually be dealt with by a direct approach to the relevant personnel, and/or the issue of an alert to all personnel.
General Protective Measures
Users of display-screen equipment (DSE), including laptop and office-based workstations, must assess whether it satisfies the legislation concerning eyestrain and posture. A written assessment of each station must be made at the start of a project or when circumstances change. An external keyboard and mouse must be used with a laptop computer. DSE training and the form for making DSE assessments is available on DUO under My Organisations & Online Training (“Health and Safety All Staff Training”). See also the UHSS website (UHSS/Topic A-Z/DSE).
If you experience visual discomfort when using DSE make an appointment with Occupational Health ([email protected], Tel. 42662).
The moving of a load by hand must comply with regulations governing manual operations. The need to move loads by hand should be minimised, mechanical aids must be used fully and a load that is very bulky or heavy must be assessed in writing before it is lifted or moved. See Appendix D.
Slips and trips are a common cause of workplace injuries. The Department has management systems in place to eliminate or minimise the risks from slips and trips. These risks must also be considered during planning, construction and refurbishment or any changes of use within buildings.
The reduction of injuries from slips, trips and falls can only be achieved when managers, staff and students are committed to taking personal responsibility. In order to achieve this the Department will:
- provide a safe working environment for users of Chemistry facilities that is free from slip and trip hazards, as far as reasonably practicable;
- adequately control or reduce the risk of slips and trips, by a combination of a safe environment and safe behavior;
- ensure that appropriate risk assessments and risk reduction methods are in place;
- encourage all staff and students to take personal action to reduce the risk of slips and trips as far as possible;
- ensure that there is an effective response to changing conditions such as weather and the environment, e.g. during refurbishment.
All staff and students should ensure that if a slip or trip risk is identified it is reported to a suitable manager, or Estates and Buildings (via Mr Paul Hofmann) for the matter to be addressed.
It is a legal requirement that everyone is protected from the effects of hazardous materials (the legislation comes under the title Control of Substances Hazardous to Health – COSHH for short). Users must also consider the hazards associated with substances which could cause harm by fire, explosion and similar energetic events, as required by the Dangerous Substances and Explosive Atmospheres Regulations 2002, DSEAR. The approach is comparable to that used in the COSHH Regulations for managing substances with the potential to cause harm to health (UHSS/Topic A-Z/COSHH).
The COSHH and DSEAR Liaison Officer for the Chemistry Department is Dr John Sanderson who, as Departmental Safety Coordinator, is responsible for monitoring workers’ compliance with all aspects of the Chemistry Department Health & Safety Policy. If you are to use any chemical in your work, you have to inform yourself about its toxicity and the safety precautions to be taken when acquiring, storing, using and disposing of it. THIS INFORMATION MUST BE RECORDED AND PRESERVED IN DEPARTMENTAL RECORDS (see also Code of Practice A, Part 2). A strict procedure is laid down for compliance with this section of COSHH regulations and is as follows.
Order requests for chemicals are submitted through the LabSafe system. When ordering a chemical from a supplier, a material safety data sheet (SDS) MUST be obtained from the supplier before the order is placed. Note that the ‘Global Harmonised System (GHS) of Classification and Labelling of Chemicals’ is currently being used in place of the old CHIP (R/S) system, which ceased to be legal from 1 June 2015. The hazard and precautionary statements in the SDS are included with the order information and will be associated with the material in the LabSafe database until its disposal. It is the responsibility of person placing the order to read the SDS and check that the details in the order are correct.
Your Research Supervisor checks the details of the request, including the hazard and precautionary statements and processing information, before approving the order.
Upon delivery of the chemical, staff in the Central Store will add a bar code or QR code to the container and you will be informed through LabSafe that it is available for collection.
If you are have acquired a chemical that has been:
purchased from new;
acquired from another research group in the Department (chemicals covered by an end-user agreement are not transferable);
supplied by another research group outside the Department;
you must ensure that the container has an appropriate label and transfer the chemical to your laboratory on the LabSafe database.
All compounds and materials must be kept in APPROPRIATELY LABELLED containers that are stored in an appropriate manner.
Every chemical that you intend to use must be subject to a risk assessment beforehand, either as part of the project risk assessment, or as part of a specific code of practice, or as part of a one-off experiment recorded in your laboratory notebook (see Code of Practice A, Part 2).
Each year the Department must declare chemicals used, manufactured or held in the Department which have a potential use in chemical weapons (UHSS Topic A-Z/Chemical Weapons and Drug Precursors).
Lists of scheduled chemicals can be found by following the links at:
https://www.opcw.org/chemical-weapons-convention/annexes/annex-on-chemicals/Research group leaders will be asked regularly by Mr Andrew Unwin to verify their usage. Schedule 1 chemicals require a special license and should not be used in the Department.
There are limits on the amount of Category 2 drug precursors held by the Department during a given period. (UHSS Topic A-Z/Chemical Weapons and Drug Precursors). Category 2 drug precursors should be flagged automatically during the LabSafe ordering process, but please check that this has occurred correctly before submitting the order. The Departmental Safety Coordinator is responsible for ensuring the correct paperwork is in place if limits are exceeded. Any work involving Category 1 drug precursors requires a Home Office license. Any persons requiring such a license should contact the Departmental Safety Coordinator to discuss this.
Where end-user certificates are required these should be signed by the principal investigator/group leader and copies retained by Stores.
It is a Departmental rule that all persons in laboratories, whether or not they are actually doing practical work, MUST wear safety spectacles in designated areas, and, when judged necessary, safety visors. Supervisors should ensure that all visitors, including undergraduate students, to their laboratories comply with this rule.
Persons are encouraged not to wear contact lenses when working in a laboratory. Spectacles covered with plastic eye shields or prescription safety spectacles can be used instead.
Anthony Baxter (CG010A) arranges for the provision of prescription safety spectacles for staff and students (undergraduates at their own expense).
All persons whose work takes them into laboratories where chemicals are stored or handled must wear laboratory coats. They are available from the Central Store. Laboratory coats should be stored in the laboratory in close proximity to the door. They should never be stored on the back of a chair or other piece of furnishing in the immediate vicinity of an area where experimental work is conducted.
Safety shoes are provided (at their supervisor’s expense) for all postgraduates and members of staff whose work could involve handling heavy objects, including cylinders and liquid nitrogen Dewars. All persons whose duties might lie in the Department’s laboratories and workshops must ensure that their footwear incorporates flat heels, slip-resistant soles and uppers fully enclosing the foot.
Hands at risk from exposure to chemicals or mechanical injury alone (bruising or laceration from work with heavy or rough-surfaced objects or where hot or cold objects are used) must be protected by gloves. Guidance on the protection of hands is in Code of Practice A, Part 3c.
Smoking, or the use of e-cigarettes, is not allowed in Chemistry accommodation or adjacent public-circulation areas.
In workshops and in all laboratories, hair should be secured so that it does not hang below the neck.
The following rules apply to the abatement of noise.
Radios and players of prerecorded sound may not be used in corridors and circulation areas if they speak through headphones.
Radios, and players of prerecorded sound that have open speakers, may not be used in a public area.
Audio equipment as defined above may be used in rooms not mentioned in (ii), but not to produce sound audible in adjacent rooms or public areas. As a matter of courtesy, such equipment must be switched off at the request of any occupant who objects to the noise.
Information on protecting employees from noise whilst engaged in University-related activities can be found at UHSS Topic A-Z/Noise.
Mobile phones, or other portable electronic devices for personal use, should not be taken into a teaching or research laboratory, unless permitted by covid-19 exceptions. There is a risk of contamination and of damage to both the phone and electronic equipment within the laboratory.
Covid-19. Whilst covid-19 measures are in place, mobile phones may be used in laboratories for contact tracing and other welfare measures, such as lone worker check-ins. Phones must remain in pockets when not in use and must be cleaned with an appropriate wipe on leaving the laboratory.
Mobile phones, or other portable electronic devices for personal use, should not be used in general circulation areas. It is important that users of general circulation areas are fully aware of activities in their vicinity.
No person of age ≤ 5 is allowed in Chemistry accommodation or adjacent circulation areas unless closely supervised by an adult and kept in close proximity to that adult at all times. Older children up to the minimum school leaving age must be accompanied by an adult responsible for their behaviour. For children attending organised activities (e.g. for work experience or outreach), the Department will ensure that suitable risk assessments are in place and adequate supervision is provided in line with published guidance (UHSS Topic A-Z/Children and Young Persons).
The University Radiation Protection Committee has banned the use of laser pointers with an output of > 1 mW. Users should consult the Departmental laser and non-ionising radiation officer, before use, if they have any doubts about the safety of a laser pointer. More information is at UHSS/Radiation/Non-Ionising Radiation/Guidance/Laser Pointers.
The Mechanical Workshop is in the charge of Mr Neil Holmes, who supervises the usage of its equipment by other authorised users and ensures that all moving machinery is guarded.
Liaison with Contractors and Service Staff
Mr Paul Hofmann liaises with service staff and outside contractors. He informs them of Departmental Health & Safety policy and makes them aware of any hazards or potential hazards in areas where they are working (in consultation with the appropriate research supervisor(s)). Laboratory workers should make the area safe for work and also ensure that any visitor or contractor working in their area is aware of the hazards present and is working safely (including wearing safety glasses at all times and lab coats as appropriate).
Reports of Defective Equipment and Building Hazards
Individual reports should be made by using the form on SharePoint (http://chem-sp.dur.ac.uk/sites/chemistry). Action by the Estates and Buildings Department can then be arranged.
Training/Supervision
A departmental safety induction, ‘Risk Management in Chemistry’, is given twice annually by the Departmental Safety Coordinator, with support from other members of the Safety Committee. An online version of the training for short term workers, such as visitors, is available on DUO. The induction covers basic health and safety, including: hazards vs risk; making risk assessments; waste disposal; PPE; good laboratory practice; fire safety; and emergency measures. Health and Safety Management Standard 3 gives further information on training and competency (UHSS/Topic A-Z/Training and Competency).
Undergraduate students with ≤ 3 years study who have not completed a safety induction must be accompanied at all times in the laboratory by a postdoctoral researcher or member of academic staff.
Undergraduate students undertaking 4th year research projects (MChem or MSci) who have completed a departmental safety induction may work independently, provided that other researchers are in close proximity (in addition to the lone working regulations). Outside undergraduate terms, written conformation that appropriate supervision is available, along with details of the student and the dates of work, must be sent beforehand to the Departmental Safety Coordinator and the Director of Teaching.
The training of undergraduates in good experimental technique and the appreciation of safe working is provided by academic staff during laboratory classes. Undergraduates starting their Chemistry Research Project attend the departmental safety induction. Training in the use of fire extinguishers is optional (‘opt in’). Additional project-specific training is provided by project supervisors.
All other personnel using Chemistry facilities are required to attend a departmental safety induction, and are required to receive the specialist safety training identified in the ‘training requirements’ section of the new starter (PR1) forms. Academic supervisors take responsibility for day-to-day training in safe working practices.
In advance of a planned absence from Durham of two or more working days, research supervisors must nominate another member of academic staff to provide research group supervision (‘cover’). An email outlining the cover arrangements must be sent to the replacement supervisor, group members and [email protected]. Staff members providing cover must be competent to authorise any new risk assessments required during the period for which cover is provided (see Section C, Part 4).
Asbestos
The use of asbestos is strictly forbidden in the Department of Chemistry.
Legionella
Legionella is a naturally occurring bacterium found in water systems that can produce potentially fatal pneumonia like illnesses such as Legionnaires’ disease if it is inhaled into the lungs. This can happen when it finds its way into droplets of water that become airborne, for example where water sprays from an outlet.
This can be produced in certain hot and cold water supplies and also some types of air conditioning systems.
The Director of Estates and Facilities is the Nominated Manager for the control of Legionella and ensures that formal arrangements for oversight and monitoring are in place. However, some of the responsibilities and actions rest with the Heads of Departments, Colleges and Services (or equivalent).
There is a reasonably foreseeable legionella risk in your water system if:
water is stored or re-circulated as part of the system;
the water temperature in all or part of the system is between 20-45 °C;
there are sources of nutrients, e.g. rust, sludge, scale, organic matter;
it is possible for water droplets to be produced and, if so, if they can be dispersed over a wide area, e.g. showers and spray taps; and
personnel are more susceptible to infection and could be exposed to contaminated water droplets.
Systems that may not be the direct remit of Estates and Facilities include:
some showers including safety showers;
eyewash stations/fountains;
some aspects of hot and cold water distribution systems;
saline/brine/experimental tanks; and
little-used outlets (for example remote taps) as these are not always known or accessible to Estates and Facilities.
For other systems, you should consult with Paul Hofmann and Estates and Facilities to see where the responsibility lies.
Occupational Health
Occupational Health is a 3-way partnership between an individual, their line manager and the occupational health professional and is about ensuring that the individual is fit for the job and the job is fit for the individual. You should contact occupational health if you feel that any aspect of your work is contributing to a medical condition, or a risk or COSHH assessment has indicated that health monitoring may be required (see e.g. Code of Practice A, Part 2(c)). Occupational health can be contacted by email at [email protected], Tel. 42662. Further information is available on the occupational health website: https://www.dur.ac.uk/hr/occupationalhealth/.
Information Storage
DUO (‘Chemistry Safety’ module) is used for storing shared training material such as SOPS and induction material. The ChemSafetyRecords SRS is used for the storage of records (e.g. ad hoc operating procedures and codes of practice, training records, laboratory self-inspections) and for induction material. All other document templates are available through the Chemistry Safety website.
Section E: Out of Hours Working
Out of Hours Working
Undergraduate students are not allowed in research facilities (e.g. laboratories, analytical services) outside the period 08.45 to 18.30 on Monday to Friday unless they are accompanied by a member of academic staff who has agreed to act as their supervisor.
Research workers must not undertake experimental procedures outside normal working hours (07:00 to 19:00, Monday to Friday) unless their supervisor or the Chair of the Board of Studies authorises the work. If work outside normal working hours is permitted and undertaken, another research worker (‘buddy’) must be nominated to be within earshot and aware of the experimental work. The name of the nominated person must be indicated in the out of hours record book at the Security Office (see paragraph (c) below). Hazardous work must be avoided.
Further information can be found on Health and Safety Services web site, Health and Safety Guidance 13 (UHSS/Topic A-Z/Lone Working).
Postgraduate students should normally leave the science site by 22.00. Any work between 22.00 and 07.00 needs specific permission from the supervisor and the Chair of the Board of Studies, as well as a separate risk assessment.
Covid-19. Researchers should be extra vigilant concerning the potential for lone working. Should lone working be unavoidable, the Covid-19 MS Teams App should be used to manage this scenario. If this App cannot be used, consult the Safety Chair (Dr John Sanderson) for alternative measures. For more information, consult in Appendix I.
Postgraduate students and staff members must use the entrance next to the Security Office (red atrium) and record their presence in the Departmental out of hours book (located in the Security Office) if:
arrival is before 07:00 on a normal working day (Monday to Friday);
arrival is after 19:00 on a normal working day;
it is a weekend or other statutory day when the Department is closed.
A person who is already in the Department at 19.00 on a normal working day and plans to stay in the Department beyond that time, must telephone the Security Office (ext 42222) to report their whereabouts and to name any undergraduate students being supervised.
Covid-19. Out of hours working should not be undertaken without approval from the Safety Committee.
Apparatus Working Overnight
Apparatus working overnight. Yellow forms, available in CG018, must be completed to give information about the services used, the nature of the experiment, emergency procedure and an emergency contact. The yellow card is left in the card holder on the laboratory door and the fume cupboard light housing the experiment must be left on. Authorisation by a member of academic staff is required.
In addition, a green form, available in CG018, must be completed to give information about the services that are being used that would present a safety risk in the event of their failure. The card must include the name of the research supervisor to contact in the event of a service failure (no other contact details are necessary). The green card is left in a separate card holder on the laboratory door. More information is on the Chemistry Safety website under Key Topics/Out of Hours Working.
Covid-19. Overnight experiments should be avoided unless absolutely necessary whilst covid-19 measures are in place. Should apparatus need to run overnight, the following protocol should be followed:
Follow the usual rules (set up must be stable for at least half an hour before you leave, temp. regulation on hotplates, condenser tubing secured and flow at minimum needed etc).;
Complete the yellow form as normal, in pencil if possible. Photograph both sides, then wipe/disinfect the form and place it in the door holder.
Photograph the experimental set up.
Send all photos (both sides of yellow form, plus set up) to the supervisor (or person who is providing research cover).
If the authoriser is satisfied that the set up is safe, an email should be sent stating this to [email protected], including the photographs (set up + yellow forms) as attachments. If the authoriser is not satisfied, steps (i) to (iv) should be repeated.
Permanently running electrical equipment. Permanent running cards should be displayed on laboratory doors. The Security Office has a list of staff responsible for each room and their contact details. A shut down procedure for each item mentioned on the card should be displayed in a prominent position so that anyone should be able to shut down the instrument safely.
Section F: Electrical Safety
Electrical Safety
Electrical safety is managed in the Department by working to the policies set out on the Health and Safety Service web page (UHSS/Topic A-Z/Portable Electric Equipment), and Departmental codes of practice.
Live Electrical Working is only allowed to be undertaken by competent persons who have received training in Live Electrical Work and who agree to follow the Safety Policy guidance (Special Code of Practice G, Dr Bryan Denton). A copy of this is kept in the Electronics Workshop and is available on the Chemistry Safety website (under Policy/Special Codes of Practice).
Each user is responsible for assessing equipment before using it, and must not use equipment with cable, plug or mechanics looking unsound or with a test-expiry date that predates the date of use. Equipment not fit for use must be taken immediately to the electrical/electronic workshop MC009 for repair. Users must comply with any requests made by workshop staff concerning their equipment.
High risk items, including block adapter plugs, plug in air fresheners and fan heaters, must not be used in offices. Toasters and other cooking items may only be used in designated food preparation areas.
Extension leads must not be daisy chained or overloaded.
Dr Bryan Denton schedules regular testing of all electrical equipment (some 5000+ items). A test comprises: a check of insulation; earth continuity and mechanical soundness. The user is responsible for ensuring all electrical equipment is available in a clean state for the agreed period of testing.
The testing of computers connected to equipment in laboratories is carried out by Mr Omer Ekinoglu. New computers for offices are inspected by CIS on purchase.
Visitors and Undergraduates must ensure that any chargers used for portable devices are inspected before use in the Department.
PAT procedure for Designated Person
For Portable Appliance Test (PAT) purposes, each laboratory supervisor nominates a ‘designated person’ whose job is to help testing to proceed efficiently and safely. The following procedure is required to ensure compliance.
In line with the Chemistry Department Health and Safety Policy, it is an accepted rule that all persons have a responsibility to ensure that their work does not create a risk for any other person working nearby. It is therefore required that during Portable Appliance Testing (PAT) all work should be suspended, and that all electrical equipment (including all equipment in cupboards), should be made safe.
This means that it should be switched off and disconnected from the mains supply, any chemical or other contamination should be removed, and the equipment should be placed in a position in the lab where the test person can easily and fully examine it and carry out the required test procedures to assess the safety of that item. Any equipment that is in use or cannot be switched off shall be labelled to show that it was not available for test on the due date, and it will be the responsibility of the user to ensure that it is tested as soon as possible afterwards. It is accepted that some equipment cannot be switched off, and the owner should notify the electronics workshop (MC009, ext. 42015) when it is switched off for maintenance, or other reason and testing can be carried out on request at this time. Equipment that is not used or is in storage will be labelled as Out Of Commission and disabled until such time as it is required for use, when it MUST be tested before use.
Important note:
If during testing the designated person or substitute is not present, then the work will immediately stop for safety reasons.
Rescheduling of testing of the remainder of the equipment will depend on workload, and may result in equipment being switched off in the interim due to expiry of test date.
*Please make the test person aware of any equipment which you know to be unsafe or not working correctly, and as he is not a chemist please make him aware of any specific hazards in the lab.
The Electrical/Electronics Workshop is in the charge of Dr Bryan Denton, who supervises the usage of its equipment by other authorised users.
Covid-19. Anyone needing the services of the electrical workshop are advised to contact Dr Denton in the first instance.
Section G: Work in Confined Spaces
Definition of a Confined Space
Under the Confined Spaces Regulations (1997), a confined space is defined as “any place… which, by virtue of its enclosed nature, there arises a reasonably foreseeable specified risk”. For work in the Chemistry department, the predominant risk is loss of consciousness or asphyxiation arising from gases, fumes, vapours, or lack of oxygen in wholly or mostly enclosed spaces.
Atmospheres containing < 18% oxygen are potentially dangerous. The risk of unconsciousness followed by brain damage or death due to asphyxia is greatly increased at oxygen concentrations below 10%. Concentrations of CO2 of 10% will lead to loss of consciousness in a few minutes. Concentrations of CO2 of 20% and above are an immediate risk to life even when oxygen levels are normal.
Key factors to consider are the potential volumes of gas or vapour that could be released and the likely rate of release. For example, most cryogenic liquids have an expansion ratio close to 1:700, i.e. 1 litre of liquid will produce approximately 700 litres of gas. During transfer from a non-pressurised Dewar, 10% of a cryogenic liquid will typically be lost as gas. For compressed gases, guidelines on how to calculate the effects on oxygen content for various scenarios are published by the British Compressed Gas Association (note GN11, 2002, http://www.bcga.co.uk/pages/index.cfm?page_id=73).
In most laboratories in the Chemistry department, fume cupboards and make-up air prevent the accumulation of toxic fumes or vapours. Such ventilated spaces are not confined. Two scenarios that can produce confined spaces are:
a small room or space without significant ventilation in which chemicals, cryogens, or laboratory gases are used and operations are conducted with the door and windows closed (even if this not essential), e.g. some of the small rooms that open onto the corridors in the main building;
a space or room without ventilation that requires the door to be closed during normal operation, e.g. controlled temperature rooms and lifts.
Protocols for Work in Confined Spaces
Before beginning work in a confined space, consideration should be given to alternative modes of operation that eliminate or reduce the risks. Note that in the instance described in 1(a) above, the simplest solution is to work with the door or a window open, so that the room is no longer classed as confined.
Work in a confined space with hazardous or toxic chemicals that are released into the atmosphere requires respiratory protection. The Chemistry department has no provision for work of this nature. This work is therefore not permitted in a confined space in the department.
In a confined space, work that produces small amounts of volatile substances may be conducted safely using a recirculating or ductless fume hood fitted with a suitable filter. It is essential that the filter material is appropriate to absorb or filter for the substances produced, and has ample capacity for the quantities of substance produced. Filters must be inspected and changed regularly. Work must not be undertaken if a filter is out of date or unsuitable in any other way.
In instances where the use of gases, cryogens or chemicals in a confined space is unavoidable, a code of practice should be written by the staff member(s) responsible for the space in consultation with the Departmental Safety Coordinator and must describe the procedures and protocols to be followed for safe working. This should include an assessment of the potential volumes of gas released and consequently the potential for a dangerous atmosphere to result. The use of oxygen monitors should be considered, if appropriate. The code of practice should be placed on the entry point to the space so that it is seen by all persons who enter the space and anyone who might be called to the room during an emergency procedure.
Emergency Measures
Anyone discovering a person who is unconscious in a confined space must not enter the room. The emergency services should be called immediately, before seeking assistance from the Chemical Hazard Response Team (breathing apparatus) (Section B).
Section H: Manual Handling
Manual handling refers to an activity that requires manual effort to be applied to a load being pushed, pulled, picked up, lowered down, carried, supported or otherwise moved. Activities involving equipment used to reduce the effort are included, e.g. the use of trolleys, barrows and levers. A number of loads that are moved within the Department may require assessment under the manual handling regulations, depending on how they are manipulated e.g. Dewars of cryogenic liquids, gas cylinders, centrifuge rotors and drums of silica. Additional information is in Appendix D and online at UHSS Topic A-Z/Manual Handling.
Responsibilities
All Employees: follow the method agreed for the particular task and observe the rules.
Supervisors: consider handling implications before ordering new equipment and taking delivery. Monitor tasks to ensure that approved methods are followed and that relevant rules are obeyed.
Chair of the Board of Studies in Chemistry: appoint persons to be assessors for significant manual handling operations. Ensure that formal assessments are carried out and reviewed on a regular basis.
Handling Assessors: carry out assessments in accordance with the training provided by the University Health and Safety Service.
Assessment Officers: organise awareness sessions. Keep a record of formal assessments and make them available to all interested parties.
Rules For Persons Involved In Manual Handling
Examine the load to be moved for hazards and study how best to tackle the problem. This will mean giving consideration to the height, shape, and position of the load.
Follow the appropriate safe system of work in which you have been trained for the handling of loads and use kinetic handling techniques where appropriate to avoid injury.
Before moving a load, ensure that it does not obstruct your view.
Inform your immediate supervisor/line manager of any personal condition that may require review of your manual handling activities, e.g. medical condition, pregnancy.
Consider whether there will be any obstacles in your path, any slipping, tripping or falling hazards, any stairways to be negotiated.
If there is any doubt as to the correct manual handling arrangement, seek advice from your immediate supervisor or line manager.
Section I: Waste Disposal
Waste Disposal
The Department has strict procedures for the disposal of liquid waste, solid waste, waste gases, unwanted chemicals and waste equipment. The arrangements are designed to comply with the University’s Health & Safety policy, and the practices described are binding on all workers in the Department.
Some substances, termed ‘Red List Substances’, must never be disposed of down the drain. These are listed in Appendix G.
A flow chart should be located prominently in each laboratory.
When staff and/or research workers leave the Department it is their responsibility to clear away or destroy unwanted chemicals.
LIQUID WASTE
The Department’s non-radioactive liquid waste is handled in four categories:
(A) aqueous liquids;
(B) non-aqueous liquids that are miscible with water;
(C) non-aqueous liquids immiscible with water that give non-poisonous gases when burned;
(D) non-aqueous liquids immiscible with water that give poisonous gases when burned.
(Dr Gary Sharples oversees the disposal of all radioactive liquid waste.)
The following procedures should be used by all persons in the Department needing to dispose of liquid waste.
Aqueous liquids. Each person producing aqueous waste must render it harmless and close to pH neutral before disposing down a laboratory sink.
If the solute is known to be harmful it should be either:
treated chemically by a standard method (e.g. cyanide with 15% aqueous hypochlorite) to render the solute relatively harmless. Any precipitate separated and dealt with as ‘Lab Smalls’ solid waste. Remaining solute to be returned to the waste store in a suitable container – to be bulked with aqueous toxic / heavy metals waste;
or, if valuable (e.g. precious metals), concentrated, labelled and retained for specialist precious metals recovery.
If the solute is unknown it should be returned to the waste store in a labelled 2.5 litre Winchester bottle only. Labels are available from stores.
If in doubt, the Waste Disposal Coordinator, Dr John Sanderson (CG112), should be consulted.
Non-aqueous liquids miscible with water. Such liquids (e.g. ethanoic acid, propanone, ethanol) should be diluted at least tenfold with water and poured down a laboratory fumehood sink, if the nature of the solute allows. Liquids hydrolysed by water should be treated similarly. ‘B’ Waste considered toxic or harmful to the environment should be reclassified as either ‘C’ or ‘D’ waste, depending on whether it contains halogens or sulfur, and it should then be labelled and treated as this type of liquid waste. Large volumes of waste (> 100 ml), e.g. from high performance chromatography systems, should be taken to the solvent waste store in a Winchester labelled as ‘C’ or ‘D’ waste (plus lab number and group initials).
Non-aqueous liquids immiscible with water that give non-poisonous gases when burned. All of the common water-immiscible organic solvents containing only the elements carbon, hydrogen, nitrogen, and oxygen are in this category. Liquid waste of this type is retained for incineration. The temporary storage of the waste is supervised by the Safety and Research Technician and Mr Douglas Carswell in the waste store.
Each laboratory should provide a ‘C’ labelled glass Winchester for this category of waste. This waste bottle should be stored within a fume hood, within a spill tray or leakproof solvent carrier wherever possible. Red colour-coded ‘C’ waste labels are available from stores. They must be adhered to the Winchester bottle and filled-in with lab number and group initials.
Everyone who adds waste to a Winchester should take all reasonable steps to ensure that the solute in the waste is of very low chemical reactivity or of low concentration: waste that might fail to meet those specifications must be notified to the member of academic staff associated most closely with the work that produced the waste. For researchers producing significant volumes of waste, personal waste Winchesters are recommended.
It is recommended that a large plastic funnel be used in the neck of the bottle in place of a stopper, and left there until the bottle is ready for transfer to the waste store. The use of such a funnel provides an escape route for potential build-up of gases in the event of unanticipated chemical incompatibilities. Winchesters should not be stoppered until they are ¾ full, whereupon they should be stoppered and brought to the waste store in a Winchester carrier.
Waste Winchesters should be brought to the waste solvent store at either 09:30 – 09:45 or 14:15 – 14:30 when someone will be available to receive it. The waste bottle should be labelled with its category, and your group name or laboratory number. Under no circumstances should waste of any description be left unattended at the waste store. The Safety and Research Technician and Mr Douglas Carswell arrange the temporary storage of bottles pending their transportation by a waste-disposal organisation to a special site for incineration.
Note that any aqueous acids/alkalis MUST be separated from ‘C’ waste prior to disposal via this route. If necessary, use a separating funnel to separate off the aqueous phase and dispose of it separately according to route A above.
Non-aqueous liquids immiscible with water that give poisonous gases when burned. All of the common water-immiscible organic solvents containing halogens or sulfur are in this category. They are accumulated separately, as they must be incinerated separately, but otherwise they should be handled as described for category-C waste in a ‘D’ labelled glass Winchester. Blue colour-coded ‘D’ waste labels are available from stores. They must be adhered to the Winchester bottle and filled-in with lab number and group initials. Again, bottles should be stored within a fume hood, within a spill tray or leakproof solvent carrier wherever possible, and should only be stoppered when ¾ full and ready for transfer to the waste store.
Any aqueous acids/alkalis MUST be separated from ‘D’ waste prior to disposal via this route. If necessary, use a separating funnel to separate off the aqueous phase and dispose of separately according to route A above.
Other types of liquid waste: The service operated by Dr Connor Sibbald and Mr Douglas Carswell is restricted to disposal of chemical waste where the procedure for disposal has been established as safe. When a research programme produces waste requiring a disposal procedure where the risk is large or unknown, the member of academic staff supervising the programme is expected to devise the procedure, in consultation with the Departmental Safety Coordinator, and to be present at the disposal.
SOLID WASTE
The Department’s non-radioactive solid waste is handled in five categories using the following procedures for disposal:
Non chemical solids:
Uncontaminated paper should be consigned to recycling bins or general purpose waste bins as appropriate. Confidential documents may be shredded in CG137 or CG160 and disposed of similarly.
Uncontaminated laboratory consumables and other chemically inert or environmentally harmless solid material (not loose powders or chemicals) are also suitable for general purpose waste bin disposal.
All solid material that is contaminated with toxic or hazardous chemicals (again not loose powders or chemicals) must be accumulated in a sealed polythene bag (A3 sized or smaller), labelled as ‘Toxic Waste’ with group identification and laboratory number. Once full, the bags should be moved to a yellow hazardous waste bin in the laboratory and not allowed to accumulate in fume cupboards. Yellow bins should not be overfilled, but the yellow bags may be transported to the waste store during the waste store opening times, whether almost full or almost empty.
Glass:
Glassware that is broken should be decontaminated (washed with water or solvent) and repaired or salvaged if possible. If washed with solvent, please ensure that the glassware is dry before leaving the laboratory. Clean non-repairable glassware or redundant empty glass containers with all labels removed or defaced should be consigned to a glass bin for recycling.
Metal sharps:
All redundant, small metal items that are capable of inflicting a puncture wound, (e.g. a syringe needle, a razor blade, a scalpel, a metal pipette tip) should be rinsed if contaminated and then discarded into the a yellow plastic ‘Sharps Bin’. After cleaning, needles may be disposed of whilst still attached to disposable syringes. Plastic pipette tips can also be disposed of in sharps bins. Sharps bins should be positioned on a solid surface, not balanced on other objects, and preferably located towards the rear of a fume hood. When three-quarters full they should be sealed with the attached plastic flap and returned to the waste store at the appropriate time for specialist disposal and replacement. See also Code of Practice A, Part 7.
Non commercial toxic solids:
Most toxic solids can be disposed of by one of the following methods:
chemical treatment to give a harmless precipitate, or a harmless water miscible solution;
dissolution in water before transfer to the waste store in a suitable container to be bulked with aqueous toxic/heavy metals waste;
dissolution in an organic solvent to give category ‘C’ or ‘D’ liquid waste.
A more expensive disposal route for insoluble solid chemical waste that cannot be disposed of by other means, such as aluminium backed TLC plates and chemicals held in glass or plastic containers or in zip-lock polythene bags, is to collect the waste in a clear sealed polythene bag (approx. A4 sized or smaller) that is labelled as ‘Lab Smalls’ with group identification and laboratory number and to transfer the bag to the waste store at the appropriate time.
Used silica:
Individuals using column silica should retain all used material separately in a fume hood, remove all traces of flammable solvent (e.g. by evaporation) and then collect the used silica in a sealed polythene bag (A4 sized or smaller). This bag should be labelled as ‘Silica’, with group identification and laboratory number, before transfer to the waste store at the appropriate time. Alternatively, bags of used silica can be accumulated in the original 50 litre shipping drums, but for safety and cost reasons it is still essential that no flammable solvent vapours are present. Loose used silica must not be placed in 50 litre drums.
UNWANTED COMMERCIAL CHEMICALS
All chemicals, (liquids, solids and gases) in containers or cylinders that retain the commercial manufacturer’s label and specification should in the first instance be advertised internally and the LabSafe database updated if the material is transferred to another laboratory.
Remaining containers of chemicals can often then be economically reduced in number by utilising existing disposal procedures as appropriate (Parts 2 and 3, above).
A final inventory of any outstanding items is then prepared and submitted to the waste store for eventual specialist disposal. In the first instance, please contact Mr Douglas Carswell for assistance. Individual commercial chemicals can be disposed of by this route at any time.
Empty containers can be disposed of by the normal routes only if they have been washed free of their former contents, caps or lids removed and all labels defaced or removed.
In general, the Department expects each research worker, in consultation with their research supervisor, to treat the disposal of unwanted reaction products as an essential part of each piece of experimental work undertaken. The Department is not equipped to undertake disposal of outdated research samples and other unwanted or unlabelled material.
A research supervisor or the Chemistry Health & Safety Coordinator should be consulted in dubious cases, or when dealing with the following solids:
- calcium carbide and other substances that in contact with water liberate an insoluble gas;
- mercury, cadmium and their compounds;
- cyclic chlorocarbons;
- organotin compounds;
- other schedule-1 solids.
WASTE GASES
Waste gases are extracted and discharged from the Chemistry Building at roof level by roof-mounted electromechanical fans acting on ducts. Most laboratories have an independent system of fume cupboards served by the roof-mounted fans with their own variable-volume supply of fresh air.
A plenum system of ducts, fans and grilles brings outside air into the Building at basement level, warms the air and circulates it to heat offices and freshen the respiratory atmosphere. In rare weather conditions, a small proportion of waste air can be drawn back into the basement or into rooms with open windows. Consequently, the fume-cupboard extract system should be treated as a secondary method for removing harmful waste gases arising from the handling of chemicals, or evolved during a reaction. The primary method should be part of the equipment used for the handling. For example:
- gas evolved from a chemical reaction or released from a bottle should be passed through a solvent or reagent in a trap (“scrubbed”) so that a negligible proportion of the gas enters the fume cupboard;
- an all-glass ampoule of volatile liquid should be cooled to give a low rate of evaporation when opened to the atmosphere of a fume cupboard;
- exhaust gases from a vacuum pump vented to a fume cupboard should be checked regularly for contamination and the oil changed where appropriate.
If any vented gas can be smelled outside the Department a public nuisance exists and the Department risks a ban on the work producing the smell.
BIOLOGICAL WASTE
Biological waste is dealt with using a specific protocol. Details can be found in Special Code of Practice K, Biological Material Safety Policy.
ELECTRICAL ITEMS
Disposal regulations mean that the University is charged for the disposal of electrical goods.
Any electrical goods that are no longer required should be decontaminated so as to be free of any chemical residues. All mains operated equipment that has been used in the Department has a barcode sticker, which is used to identify the item for electrical safety testing purposes. This sticker should be removed and returned to Dr Bryan Denton in the electrical workshop so that the item can be struck off the inventory.
Waste electrical and electronic equipment should be disposed of according to University regulations as follows:
WEEE Procedure Colleges/Departments
For all items other than computers and related hardware, contact Gary Southern ([email protected]).
For computers and related hardware, contact CIS via the service desk ([email protected]).
COVID-19
Appendix I should he consulted for interim waste disposal measures during the covid-19 pandemic.
Section J: Policy Monitoring and Review
A Safety Audit is performed each year by Mr Paul Hofmann, who reports to the Safety Committee. Any repairs or maintenance requests are reported to Mr Hofmann (CG127C), the member of technical staff who deals with building-maintenance workers. The list of items checked is in Appendix B.
A safety inspection of part of the Chemistry accommodation is carried out in each of the three University terms, such that the entire accommodation is inspected annually. Responsible persons are notified of deficiencies and asked to respond within 10 working days. A report of each inspection is sent to the University Health & Safety Adviser. In cases where significant deficiencies are found (e.g. a risk of serious injury) the inspection team will make more frequent visits to ensure that the policies are being complied with.
Annual ‘Tidy Up’
One day each year, usually on a set date in September, is reserved for carrying out departmental housekeeping, including: transfer or disposal of unwanted chemicals; chemical database checks; disposal of unwanted paper documents; removal of clutter from all areas of the department; and self-checks on the safety provision and signage in laboratories and offices. These self-checks will be used to identify matters that need attention and initiate remedial action.
Annual Review of Policy and Codes of Practice
There is University management standard on Monitoring and Review (MS6, UHSS Topic A-Z/Monitor and Review).
The Safety Committee meets 3 times annually and monitors progress against health and safety objectives and plans. The committee receives reports of Health and Safety meetings, Departmental Health and Safety Inspections, Trade Union Health and Safety inspections, Accident and Incident Data, Occupational Health Referrals and notable Health and Safety activities. The minutes of this committee are used to inform changes to the policy document and Action Plan on an ongoing basis.
The Action Plan, and the Chemistry Health and Safety policy, codes of practice and appendices are reviewed annually by the Departmental Safety Coordinator and Secretary to the Safety Committee and are available on the Chemistry Safety website. The date of the next review is 31 July 2018. Policy and Action Plan amendments made before this date will be made available on the Chemistry Safety website.
Major Review of Policy and Codes of Practice
A major review of the policy is undertaken each time a new Chair of the Board of Studies is appointed, normally once every 3 years. The review is led by the Chair of the Safety Committee (in consultation with committee members) and receives input from the Chair of the Board of Studies, key representatives of technical support staff, and the Chemistry lead contact from UHSS. The review covers: changes in University policy; major changes to legislation; the structure of the safety policy document and changes to the general risk assessment. The date of the last major review was 1 August 2017.
Section K: General Codes of Practice for Laboratory Work
These codes of practice are updated annually by designated members of staff with experience of the relevant protocols. It is expected that the practices described by these codes will be adhered to when conducting work in the Department. Specific training in these codes of practice is not required beyond the safety induction. Signature of the policy document indicates agreement to their terms.
List of codes:
Code of Practice A: Good Laboratory Practice
Code of Practice B: Procedure for Obtaining Solvent
Code of Practice C: Peroxides
Code of Practice D: Vacuum Line Procedures
Code of Practice E: Use of Cryogens
Code of Practice F: Solvent Degassing
Code of Practice G: Disposal of Lithium Aluminium Hydride and Grignard Reagents
Code of Practice H: Carcinogens
Code of Practice I: Guidance Notes for the Use of Mercury and its Compounds
Code of Practice J: Use of the Cold Room (CG211)
Section L: Special Codes of Practice for Laboratory Work
These codes of practice are updated annually (usually in October) by designated members of staff with experience of the relevant protocols. Specific training in these codes of practice is a requirement and must be completed annually. The designated staff member is responsible for organising the training and maintaining signed records of that training. Signatories to the code of practice agree that the code has been understood and will be followed. The performing of work in these codes by untrained individuals is unauthorised.
Special Experimental Procedures. Special codes of practice (S-COP) or standard operating procedures (SOPs) to be followed are listed below and are updated by the person stated, in consultation with the Departmental Safety Coordinator. The date of the last revision is shown. Please check the Chemistry Safety web pages for revisions made since this policy document was generated.
Notes of guidance for the use of cyanides (10/09/2019)
High-pressure laboratory (15/09/2017)
Reactions in Carius tubes (15/09/2017)
Perchloric acid (13/09/2019)
Elemental fluorine and anhydrous hydrogen fluoride (16/09/2019)
X-ray diffractometry (15/09/2017)
Live electrical work (13/09/2019)
Safe use of carbon monoxide gas at low pressures in synthetic laboratories (15/09/2017)
Use of unsealed sources of radioactive materials (19/09/2019)
Laser safety policy (13/09/2019)
Biological materials safety policy (13/09/2019)
Piranha (hydrogen peroxide/sulfuric acid) (14/09/2019)
Hazardous material release involving the use of SC-B/A (10/09/2018)
(S-COP A – Dr Connor Sibbald)
(S-COP B – suspended)
(S-COP C – suspended)
(S-COP D – Dr John Sanderson)
(S-COP E – Prof Graham Sandford)
(S-COP F – Dr Ehmke Pohl)
(S-COP G – Dr Bryan Denton)
(S-COP H – suspended)
(S-COP I – Dr Gary Sharples)
(S-COP J – Dr Eckart Wrede)
(S-COP K – Dr Gary Sharples)
(S-COP L – Prof Andrew Beeby)
(S-COP M – Dr John Sanderson)
The rules below apply to the use of cyanides and Schedule 1 substances.
Persons intending to use cyanides (CN– compounds and HCN) must:
- read and complete Special Code of Practice A;
- comply with legal requirements for the storage of scheduled poisons;
- familiarise themselves with the location of medical oxygen (outside CG004 and CG209);
- inform a specialist first aider (see Special Code of Practice A) when work with cyanide is being carried out.
All Schedule 1 substances must be stored in a suitable secure place and an inventory kept of their usage.
Section M: Appendices
List of appendices:
Appendix A: Safety Committee Membership
Appendix B: Duties Carried Out by the Chemistry Safety Auditor
Appendix C: General Hazard Assessment
Appendix D: Manual Handling Regulations
Appendix E: Chemical Glove Performance Standards
Appendix F: Absorbent Materials in Spill Kits
Appendix G: Red List Substances
Appendix H: Diphoterine®